Mud cooling systems are an essential technology in the oil and gas industry, particularly in drilling operations where temperature regulation of drilling mud is critical. Drilling mud, or drilling fluid, plays a vital role in lubricating the drill bit, transporting rock cuttings to the surface, and stabilizing wellbore pressure. However, friction and geothermal heat can raise the mud’s temperature, reducing its viscosity and effectiveness. Mud cooling systems address this by maintaining optimal mud temperatures, enhancing drilling efficiency, and preventing equipment failures.

Purpose and Importance
The primary purpose of a mud cooling system is to cool drilling mud that becomes heated during operations. High temperatures can degrade the mud’s properties, leading to inefficiencies or even dangerous situations like blowouts. By keeping the mud within a suitable temperature range, these systems ensure smooth drilling, reduce wear on equipment, and minimize downtime. For example, in deepwater drilling in regions like the Gulf of Mexico, mud cooling systems are indispensable due to the extreme heat encountered at depth.
Components and Operation
A typical mud cooling system includes three main components:
- Heat Exchanger: Transfers heat from the hot mud to a cooling medium.
- Cooling Medium: Usually water or air, depending on availability and environmental conditions.
- Circulation System: Pumps the mud through the heat exchanger and back into the wellbore.
In operation, hot mud flows into the heat exchanger, where it releases heat to the cooling medium—say, water cooled by a refrigeration unit. The cooled mud then returns to the wellbore, while the warmed medium is either discharged or recycled. The system’s effectiveness is often measured by the temperature differential (the difference between incoming and outgoing mud temperatures) and the flow rate of both mud and cooling medium.
Types of Mud Cooling Systems
Mud cooling systems come in two main types: direct and indirect. Here’s a comparison:
Feature | Direct Cooling System | Indirect Cooling System |
---|---|---|
Contact | Direct contact between mud and medium | Uses a secondary fluid for heat transfer |
Efficiency | Higher due to direct heat exchange | Lower due to extra step |
Maintenance | More frequent due to contamination risks | Less maintenance needed |
Cost | Lower initial cost | Higher due to additional components |
Direct systems are simpler and more efficient but may require more upkeep, while indirect systems offer better separation at a higher cost.
Benefits and Integration
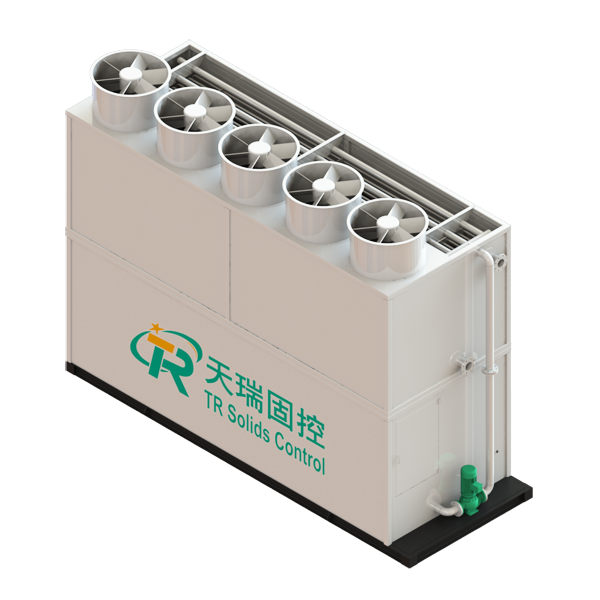
Mud cooling systems improve drilling by preventing equipment overheating, enhancing penetration rates, and reducing mud replacement costs. They integrate seamlessly with mud management systems, including mud tanks and shale shakers, for cohesive operation. In arid regions, air-based cooling might be preferred, while water-based systems dominate where resources allow.
Environmental and Maintenance Considerations
While effective, these systems pose environmental challenges, particularly with cooling medium disposal. Closed-loop systems that recycle water are gaining traction to reduce waste. Maintenance is also key—fouling in heat exchangers or leaks in circulation can disrupt performance. Here’s a troubleshooting guide:
Issue | Possible Cause | Solution |
---|---|---|
Reduced cooling | Fouled heat exchanger | Clean the exchanger |
Leaks | Damaged hoses | Replace components |
Inconsistent temperature | Faulty sensors | Calibrate or replace |
Regular inspections and operator training ensure reliability.
Future Outlook
Advancements in heat exchanger design and sustainable cooling mediums promise greater efficiency and lower environmental impact. As drilling ventures into harsher environments, mud cooling systems will remain vital for safety and performance.