A Mud Management System (MMS) is an essential part of the drilling operations in the oil and gas industry, ensuring that the drilling mud is efficiently handled throughout the drilling process. Drilling mud, also known as drilling fluid, is a mixture of water, clay, chemicals, and other substances, and is used to cool and lubricate the drill bit, control pressure, and transport cuttings to the surface. A Mud Management System aims to maintain the proper properties of the drilling fluid, minimize waste, reduce costs, and ensure safety and environmental protection. This system involves several processes, including circulation, treatment, monitoring, and disposal of the mud. This article will explore the importance, components, working principles, and applications of Mud Management Systems.
Importance of Mud Management Systems
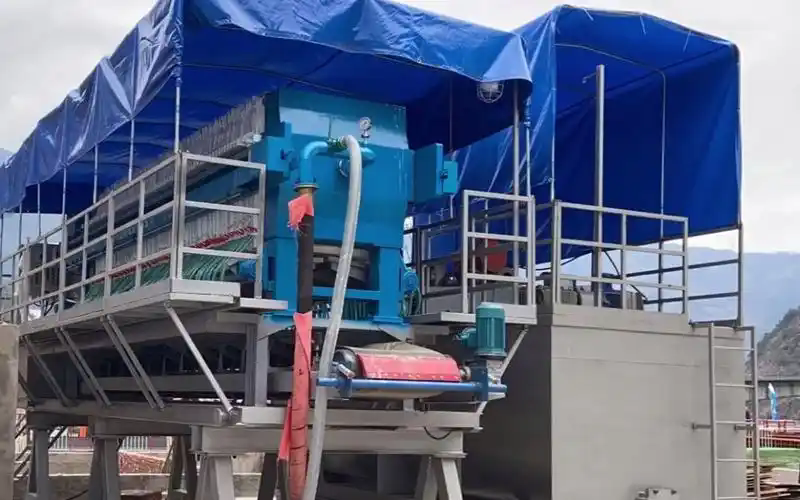
Mud Management Systems are crucial for a variety of reasons:
- Wellbore Stability: Drilling mud maintains wellbore stability by exerting hydrostatic pressure on the formation, preventing the influx of formation fluids and controlling pressure. This is particularly important for deepwater and high-pressure wells.
- Controlling Pressure: By providing pressure control, MMS helps prevent dangerous incidents like kick events, which can lead to blowouts if not managed properly. The system keeps the pressure within safe limits, protecting the wellbore.
- Efficient Drilling: The system helps ensure that the mud properties, such as viscosity, density, and fluid loss, remain within specified ranges. Proper mud management optimizes the rate of penetration (ROP) of the drill bit and helps minimize downtime due to equipment failure or hole problems.
- Environmental Protection: A well-maintained mud management system minimizes the environmental impact of drilling operations by efficiently treating and disposing of used mud. Reducing the amount of waste and avoiding contamination of surrounding land and water is essential for compliance with environmental regulations.
- Cost Efficiency: By recycling and reusing drilling mud, MMS reduces the need to purchase new mud, thus lowering operational costs. Efficient mud management also minimizes the frequency of mud disposal and the associated costs.
Components of a Mud Management System
A Mud Management System consists of several interconnected components, each playing a unique role in the management and treatment of drilling mud. The main components include:
Component | Function |
---|---|
Mud Circulation System | Circulates the drilling mud through the wellbore, allowing it to perform its functions. |
Mud Tanks | Stores and separates different phases of the mud. |
Mud Agitators | Mixes the mud to prevent solids from settling. |
Shale Shakers | Filters out large particles from the mud. |
Desanders and Desilters | Remove finer particles from the mud. |
Degassers | Remove dissolved gases, preventing issues like foam or gas influx. |
Mud Cleaner | Further removes solids to maintain the quality of the mud. |
Chemical Additives | Improve the performance of the mud, modifying its properties like viscosity. |
Mud Pumps | Circulate mud through the system, ensuring flow to the drill bit. |
Mud Circulation System
The mud circulation system is the heart of the mud management process. It continuously circulates the drilling mud through the wellbore to cool the drill bit, clean the well, and provide pressure control. It works by pumping the mud down the drill pipe and back up the annulus, carrying drill cuttings to the surface for disposal or treatment.
Mud Tanks
Mud tanks are used to store different types of drilling fluids, including the active and reserve mud. These tanks are also responsible for separating solids from liquids, allowing efficient recycling and reuse of the mud. They are equipped with various components, including agitators to mix the mud, desanders and desilters for solid removal, and degassers to remove unwanted gases.
Mud Agitators
To prevent solid particles from settling, mud agitators are employed. These devices stir the mud in the tanks, ensuring that the mixture remains uniform and that no solids accumulate at the bottom of the tank. By maintaining proper agitation, these systems ensure that the viscosity and density of the mud stay within acceptable ranges.
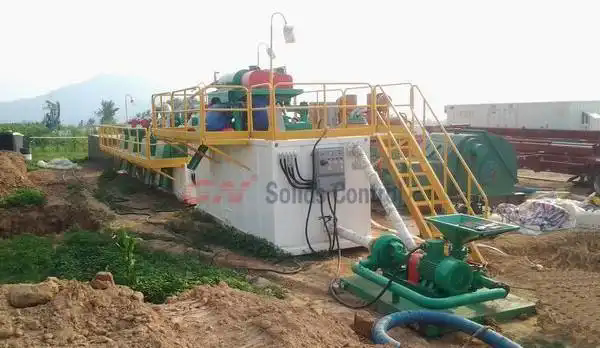
The Process of Mud Management
Mud management is a continuous process, involving several stages from initial preparation to disposal:
- Mud Preparation: At the beginning of the drilling operation, the mud is prepared according to the well's specific requirements. This involves adding chemicals and materials to create a mixture with the desired density, viscosity, and fluid loss properties.
- Circulation and Monitoring: Once the mud is prepared, it is circulated through the system. Regular monitoring of the mud properties is essential to ensure that the mud remains within the correct parameters. Parameters such as pH, viscosity, filtration rate, and density are regularly checked to ensure optimal performance.
- Solids Control: As drilling progresses, the drilling mud picks up cuttings and debris from the wellbore. The shale shaker, desander, and desilter are used to remove larger solids and finer particles, respectively. This helps maintain the mud’s properties and ensures that it can continue to carry out its functions effectively.
- Mud Treatment: To ensure that the mud remains in optimal condition, it is continuously treated by adding chemicals or additives. These additives can include flocculants, thinners, and bactericides, which improve the mud's performance, extend its lifespan, and prevent the growth of harmful bacteria.
- Waste Management: Once the mud reaches the end of its life cycle, it must be properly disposed of or recycled. The drilling waste is typically processed using cuttings dryers or centrifuges, which separate the solid waste from the liquid phase, making disposal more manageable. The treated mud can be reused, reducing the amount of waste generated.
Key Challenges in Mud Management
Effective mud management is not without challenges. The most common issues include:
- Waste Generation: Drilling mud inevitably generates waste, and managing this waste efficiently is critical for environmental and cost reasons. Technologies like cuttings dryers, centrifuges, and solids control systems are employed to mitigate this issue.
- Changes in Formation: As the drill bit penetrates different geological formations, the characteristics of the drilling fluid may need to be adjusted. The mud density may need to be increased to handle higher pressure zones, or the viscosity may need to be modified to deal with changes in the type of cuttings being produced.
- Cost of Chemicals: Chemical additives play a crucial role in mud management, but they can be costly. Efficient use of additives and recycling of mud can help reduce costs.
- Environmental Regulations: Mud management systems must comply with strict environmental regulations. This includes the safe disposal of drilling mud and the treatment of any waste by-products to prevent contamination of the surrounding environment.
Conclusion
Mud Management Systems are vital to the success of drilling operations in the oil and gas industry. They play a key role in ensuring wellbore stability, pressure control, environmental protection, and cost efficiency. The system's components work together to circulate, treat, and manage the drilling mud, ensuring that it performs its functions effectively. While there are challenges in mud management, continuous technological advancements are improving the efficiency and environmental sustainability of these systems. By optimizing the mud circulation process, controlling waste, and maintaining the quality of drilling fluids, Mud Management Systems contribute to safer and more efficient drilling operations.